Product images
The working range of the robot
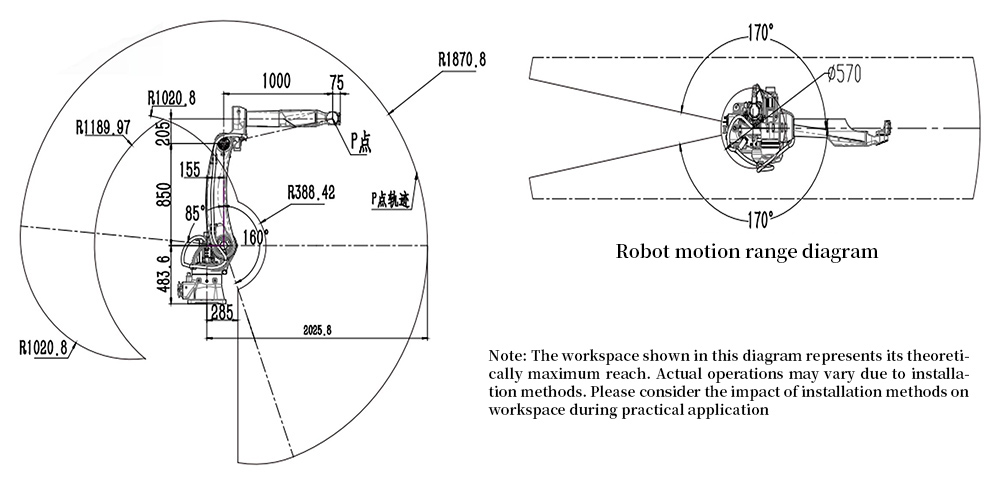
Workflow of a standalone intelligent workstation
The standalone intelligent welding workstation is equipped with a self-developed visual recognition and intelligent control system. It combines laser scanning, vision photography, and line marking to accurately locate and calculate the weld seam position.
Once the seam is detected, the system automatically adjusts the welding parameters—such as current, voltage, torch angle, and welding speed—based on the angle and dimensions of the weld. It then generates robot-executable programs to complete high-precision welding tasks.
Payload | ARC12-2000: Payload 12KG |
Maximum reach | 2025MM |
Working cycle | 7*20H |
Environmental requirements | 0-45℃ |
Workstation weight | 185KG |
Robot end effector payload | 12KG |
Welding power source | AOTAI,MEGMEET |
Operator requirements | Learning basic computer operations and mastering the GoFa Intelligent Operating System for application |
Standalone Intelligent Workstation Parameters
subitem | unit | content |
applicable scenarios | / | Suitable for node plates, purlins, cow legs, and other components, as well as small structural parts |
equipment specifications | m | 1.2*1.2*1 |
total power | KW | 15.5 |
Maximum working range | m | 2*1.2*0.3 |
average welding efficiency | m/day | 60~90(The structural types are different) |
Workflow of the Robotic Welding Workstation
1.Hoist the plate into the workstation area using an overhead crane
2.Activate the robot for automatic laser scanning
3.Generate welding/cutting programs based on scan data
4.Execute welding or cutting automatically
5.Repeat the cycle: robot scans the next piece while the operator removes the finished one and loads the next
Applicable Component Display (Partial)
This intelligent robotic workstation is ideal for welding small and mid-size structural components such as:
-
Node Plates
-
Purlins
-
Cow Legs
-
Other metal structural parts
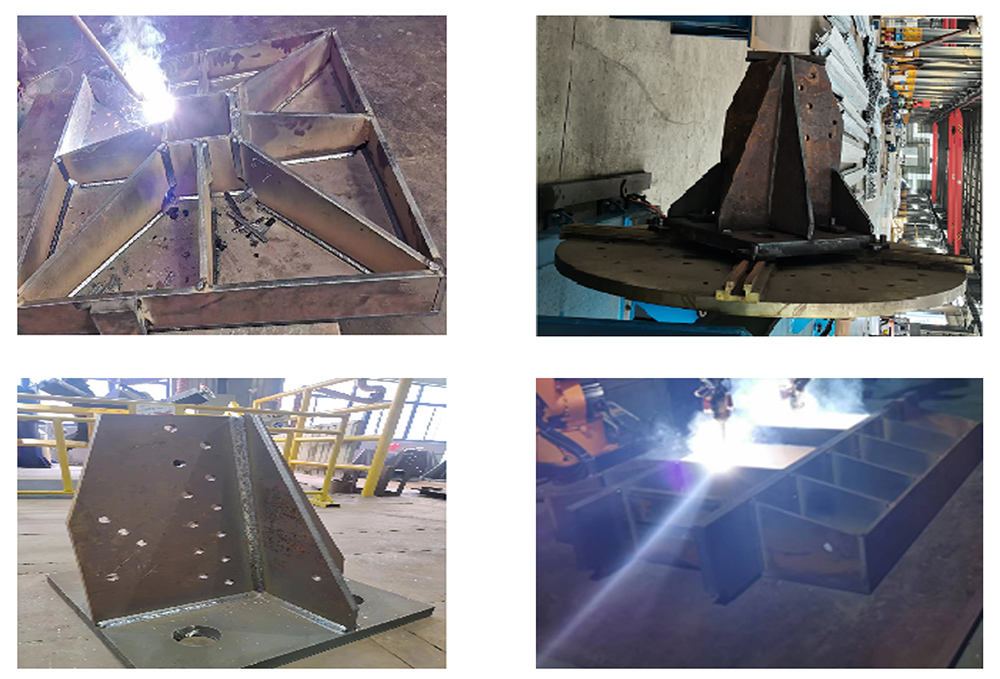